A concept widely used in the art world has a place in safety
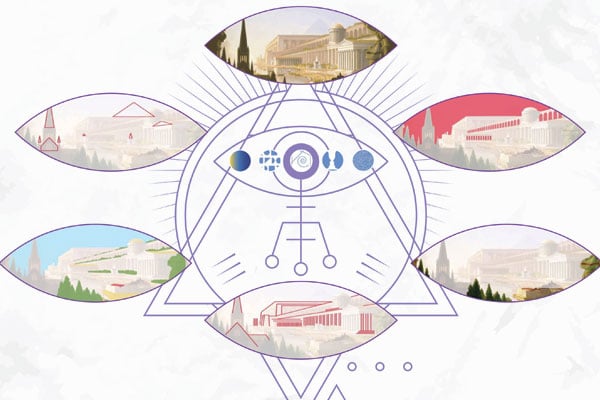
I sat back-to-back with a perfect stranger and described the small, wooden zebra that I held in my hand.
“It has a long head in the shape of an oval, with a skinny neck and a long, rectangular body. The arms are bent like boomerangs on each side,” I said to my partner, who was attempting to draw the zebra on a pad of paper.
Once our two minutes were up, we revealed the object and drawing to each other. I thought he did a pretty good job, but it was glaringly obvious the parts of the zebra I had completely failed to mention — they were notably missing from the drawing.
Doug Pontsler, chairman and managing director of COVE: Center of Visual Expertise based in Toledo, Ohio, explained to us that this exercise demonstrated the difficulty of communicating without a common language and methodical process.
Then, we moved on to a photograph of a construction site and Pontsler asked us what we noticed first. I noticed a man in a hi-vis yellow jacket, while my partner noticed the pylon in the foreground. This demonstrated that we all have a natural tendency to look for specific things that are shaped by our expectations, experiences and biases.
We were working our way through the visual literacy pavilion at the National Safety Council’s Congress and Expo in October in Houston. The exhibit was designed to teach delegates about visual literacy and explain how this concept can have a positive impact on workplace safety.
The Toledo Museum of Art describes visual literacy as being able to read, comprehend and write visual language. To be able to read visual language, an individual must scan a picture or area then observe key details in order to see the entire picture. To comprehend visual language, an individual must be able to describe the visual information in front of them and assign meaning to it. To write visual language, the individual responds to what they have seen and analyzed.
“It’s really about learning to see… It’s about what you see, what it means and then what you do,” says Pontsler, a former vice-president of EHS at Owens Corning. “A huge portion of what we do from a safety standpoint is exactly that: It’s being able to see what’s in front of us, being able to interpret what that means from a safety perspective and take the appropriate actions.”
SAFETY APPLICATIONS
Two Cummins sites in New York and Ohio trained some of its front-line workers on visual literacy as part of a pilot project with the Campbell Institute, based in Itasca, Ill. The company — which manufacturers generators and engines, and has 58,600 workers around the world — experienced a 30 per cent increase in the risk score for the area of the site that had been trained on visual literacy.
“This was great news because they’ve now identified things that they hadn’t identified or acted on before, and now they can fix those things,” Pontsler says.
As of March 2018, when the Campbell Institute checked-in with pilot participants, 225 Cummins workers at the Jamestown, N.Y. location had been trained on visual literacy. They identified 132 issues using the elements of art — line, shape, colour, texture and space — and submitted and corrected 25 hazards.
Cummins has been using visual literacy mostly for hazard identification and Kelli Smith, occupational health director, has been very pleased with the outcomes.
“We really realized that visual literacy helped employees to better see hazards that they otherwise wouldn’t be noticing on a day-to-day basis; things they are so familiar with they might just walk by,” she says.
The majority of the hazards have been identified through paying attention to line and colour. At one of its locations, workers trained in visual literacy noticed that the rise and run of some steps in the plant were not to code, the treads of the steps were run down and there was a handrail missing on one side.
“This is a work station they work around day in and day out. When they applied the visual literacy principles, they noticed the slip, trip and fall hazard,” says Smith. “Normally they would not have seen that because they were focused on other things in their visual field, but by applying those principles, it allowed that to pop out for them.”
Cummins is hoping the improvements in risk identification will allow the company to see an injury reduction over time.
Visual literacy is also very useful for incident investigations. It fosters observation skills and helps workers learn how to properly observe the area or piece of equipment where an incident occurred in order to figure out what went wrong.
“By being able to see things more completely, you can do a better job of actually understanding what happened,” says Pontsler. “After an incident occurs, it’s not unusual to hear someone say, ‘You know, we have walked by that a hundred times — or for 10 years — and we just never saw it.’”
Visual literacy can accelerate the desire to complete non-routine investigations, says Larry Masotti, director of strategic relationships at Workplace Safety and Prevention Services in Mississauga, Ont.
“When you are more skilled in perceiving and seeing more diligently, I think there’s a certain excitement in ‘Let’s go see what else we can improve in our plant or our office’ because now (they) know how to look, how to break it down.”
Workers will also feel empowered to take the time needed to identify hazards correctly under this new approach, Masotti adds.
“Things have only gotten faster, so we make some assumptions because we have to get there quicker, but if we have license in our organizational culture to say, ‘Hey, calm down, do it right, do it thoroughly and we value when you identify a hazard or a possible risk,’ I think it would increase the importance and the relevance of non-routine.”
In the case of upset conditions, anytime something goes wrong — whether it be process, mechanical or people-related — visual literacy allows workers to look at the situation through a new lens and a holistic point of view, Masotti says.
Another application for visual literacy is toolbox talks. Pontsler works with many utility companies and visual literacy skills help them to be more “effective in a dynamic way,” recognizing hazards as they are changing.
Another benefit of visual literacy is that it provides a common vocabulary. Workers learn how to describe hazards in the same way, which increases the quality of hazard reporting and incident investigations and provides the organization with more opportunity for analysis, says John Dony, director of the Campbell Institute.
“It’s sort of garbage in, garbage out. If everyone is calling something different, we will never be able to see there is a common thread. But once everyone starts calling it the same thing, we can do much better analytics on it and realize it’s a problem.”
The main reason why visual literacy is a learned skill is that individuals have many visual biases. There is so much visual data that is consumed at any given moment that individuals filter the information and only see what they deem to be important. When we look at something, we may see as little as 10 per cent and the brain is filling in the rest based on our personal experiences, says Pontsler.
Dony likens it to completing your morning routine.
“When you pour your first cup of coffee, you recognize by shape you have a coffee mug that you pulled out of the cupboard and you are pouring coffee into it, but probably aren’t taking in 100 per cent of what that mug looks like, its shape, it’s composition. If there’s a logo on it, you might not remember what it is when you turn away from it,” he says.
Individuals need to be aware of visual bias and use a step-by-step procedure to visually process a scene. Pontsler recommends taking in the big picture before zooming in on individual details. Each element of art — line, shape, colour, texture and space — should be considered during this phase. In the safety context, individuals can look for things like horizontal or curvy lines, for example.
“Maybe they see a straight line and that’s fine, such as a bracket on a shelf. Or maybe they see not-a-straight line and that’s not OK. Maybe it’s a cord running across the floor that has a loop standing up and could be a trip hazard,” Pontsler suggests.
Workers can use the element of space to determine if there is enough room to safely execute a maintenance task, or look at colours to find a hazard. For example, if there is a black organic shape on the floor, it might be an oil spill.
TRAINING
If you’re looking to train your workers in visual literacy, consider starting with the back-to-back drawing exercise that I participated in at the NSC conference. It helps workers hone their visual vocabulary and further understand the concept of visual biases.
Another useful exercise is to take a photo of the workplace, enlarge it and have workers observe and analyze the photo — something Masotti did with an automotive company. He took photos of the company’s three different plants and had workers analyze photos from opposite plants.
“It was one of the greatest learning experiences they had had because they were looking at something they hadn’t seen before and they were instructing their colleagues at another physical location about what they saw, and it worked very well,” says Masotti. “You will see things that I may not or that I have seen so many times it doesn’t even register.”
Another exercise that Dony recommends is to cut up a photo of an art work into several puzzle pieces and divide the room into small groups. Give each group two or three puzzle pieces and ask them to form an interpretation of what is going on in the full picture. Then, each group pairs up with another, so they now have five or six puzzle pieces, and they are asked to again infer what the complete scene entails.
“Chances are they’ll have new interpretations of the larger scene,” says Dony.
You can keep bringing groups together and asking them to repeat the exercise. At the end, you will reveal the entire image and debrief with the group as to the lesson they hopefully learned: It’s problematic to make assumptions based on limited information.
“What we often find at the EHS leadership level is when you get something like an incident report coming in for a very serious incident, the first batch of information coming in leads to people making assumptions right away,” he says. “The course of the investigation, the course of corrective action and maybe even the strategic focus for the organization that gets driven by the senior EHS leader might be derived on the back of that very first email that was sent about something that happened.”
The puzzle exercise can help organizations wait for information, be more patient and have more acuity not just visually, but strategically with information, Dony says.
Masotti recommends showing a safety video with each worker watching a different person or element in the video.
“Amanda, you pay attention to the lift truck; I’m going to pay attention to the pedestrian. Frank, can you pay attention to the person on the keyboard and tell us what you saw?... You will find things you haven’t seen before.”
COVE offers open two-day workshops on visual literacy at the Toledo Museum of Art every month. Trainees spend one-third of their time learning concepts in the classroom and two-thirds participating in exercises in an art gallery.
“If we do it in the workplace, you still have all this baggage around ‘Well, I am used to seeing this’ or ‘I already know what that hazard is.’ You have these expectations, these prior influences, these biases that still hang with you,” he says. “Using museum assets is a wonderful experience for people.”
COVE facilitates company-specific workshops for employers across the United States and Canada, occasionally in partnership with local museums.
THE SKEPTICS
Implementing a new training program is never without its challenges, especially one that is out of the box. Visual literacy is initially a tough sell because it sounds like a somewhat wild concept, says Dony.
“Why would a safety professional care about something that was incubated in the art world? A lot of folks in the safety field have an engineering, operations background. It’s not often that these two fields have such a Venn diagram overlap,” he says.
Smith is proof of this. She was not so sure about the idea of visual literacy at the beginning.
“When I was first approached with the idea of using art to improve the safety program, the engineering part of my brain said, ‘How’s this going to work?’ I have to admit I was a little bit skeptical on the front end, but as we went through the workshop and started to apply it, I really began to see how beneficial it could be,” she says.
Additionally, getting worker buy-in might be challenging. But Dony suggests telling workers that the training will be something a little different than the all-too-common “death by PowerPoint.”
“(Tell them) ‘We’re going to engage your brain in a different way and you will have a little fun, too,’” Dony says. “It’s not often we’re asked to flex our creative muscles at a safety meeting. It’s not often we’re asked to do something interactive and engaging like drawing — most of us haven’t drawn since we were 10 years old… It’s a breath of fresh air.”
A good strategy is to embrace the naysayers, or late adopters, and make them your champions, says Masotti. Take them for a meal or go for coffee to explain what you are trying to do. It’s helpful to have this conversation away from the workplace so they don’t have to “posture and look the part,” he says. Try to appeal to their personal motivations to help them see the value of the initiative.
“Each and every one of us has something that motivates us or makes us come to work every day; we just need to find it,” Masotti says. “It is worth the energy and investment of time — whatever it takes.”
Visual literacy training is especially well-suited for mature, high-performing companies who are looking to move the OHS needle even more.
“As you work to improve your safety performance over time, the incremental gains get more difficult and more difficult and more difficult,” says Pontsler. “High performing companies that have been at this for a while, they are really looking for new and innovative solutions to get at issues that are really hard to get at.”
This was the case for Cummins, which historically had pretty good health and safety performance, says Smith, but all the low-hanging fruit had been picked, so it was looking for another tool to get it towards its goal of zero injuries.
Visual literacy helps battle the challenges of complacency, especially for those individuals who have been at the company for a while and think they know it all and have seen it all.
“We’ve had some tough individuals who have been in the workplace for 30 years — they have been operating equipment or doing maintenance work — and they sit down in that museum and they cross their arms at the beginning and you kind of wonder if you’re going to get through to them or not, but it doesn’t take long and they are all-in,” says Pontsler.
After it implemented visual literacy training, Cummins observed an increase in employee engagement.
“In the spirit of creating an interdependent culture where employees are looking out for themselves as well as each other, identifying hazards and really being able to focus in and see those and communicate them is where we are seeing really good engagement,” Smith says.
This is one of the reasons why Cummins is planning on going global with visual literacy. Most of its workers in Canada are field service technicians and in-shop technicians who often don’t know what hazards and risks they will face job-to-job, says Smith.
“We are going to be incorporating some of these visual literacy principles into the job safety observation and job safety analysis program that is already a part of their day-to-day work,” she says. “I think it’s really going to help them be able to see what could be harmful in the tasks that they are getting ready to undertake.”
So far, in the United States, 330 employees have been trained in visual literacy and a further 6,000 will be trained this year.
Hopefully, the Cummins global workforce will be as receptive to visual literacy training as those who have already completed the program. The response was so positive, in fact, that workers have actually been asking to participate, says Smith.
“That’s what really convinced me,” she says. “In my career, there are a very limited number of times I’ve seen employees ask for health and safety training, so that was exciting.”
This article originally appeared in the April/May 2019 issue of COS.