Most significant changes revolve around PPE, fire prevention and electrical safety
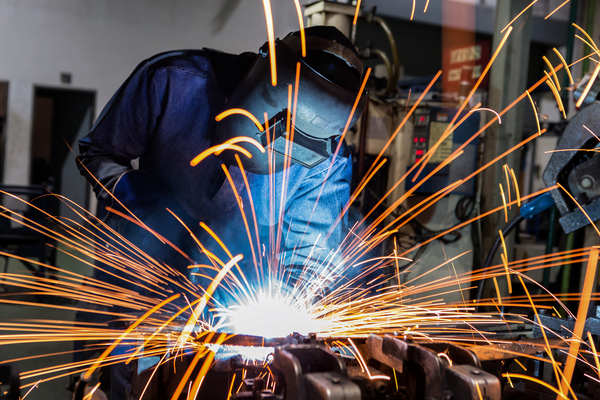
There are too many accidents, incidents and fires in Canada where welding and related activities are at the root of the event. Industry professionals, such as the volunteers who make up the Canadian Standards Association (CSA) Technical Committee for the standard W117.2, are working hard to improve the health and safety of welders and personnel in related occupations who utilize these processes.
Very recently, the seventh edition of the national standard CSA W117.2:19, Safety in Welding, Cutting and Allied Processes was published. The new edition has many progressive updates that reflect changes that have occurred in the Canadian industry since the first edition was published 45 years ago. Many of these updates are in response to the most recent reviews of injuries and fatalities within the industry. The expectation is that through continuous improvement we will be able to prevent further injuries and fatalities caused by welding and related processes (such as thermal cutting).
Although there are many updates to the current edition to the standard, the most significant changes revolve around improvements to the sections on personnel protective equipment (PPE), fire prevention and electrical safety.
PPE
In the area of PPE, there are updated recommendations in CSA W117.2:19 for the selection of protective clothing based upon the severity of the process in use. Fabric should be listed as either Class 1 for light-duty welding or Class 2 for heavier-duty welding and the performance of the fabric should be tested in accordance with ISO 11611. A guideline for selection of clothing for each class can be found in the standard.
There are also new requirements for footwear in welding/cutting environments. This came-about as the availability of the old leather work-boot has evolved to include inappropriate (for welding/cutting) low-cut athletic style safety-shoes constructed of synthetic (flammable) materials. The revised standard specifies a minimum boot height of 150 millimetres (6 inches) with an outer-shell constructed of leather or other non-flammable material along with meeting other requirements of CSA Z195:14 (Protective Footwear) including an electric shock resistance rating.
Respiratory protection requirements have also evolved as the concerns over the long-term health effects of elements such as manganese and hexavalent chromium, potentially in welding fume, have increased. Recommendations for powered air purifying respirators (PAPR), increasingly commonplace in welding and cutting operations, are now included in the latest edition.
Fire prevention
Welding, cutting and other hot-work operations in facilities or locations where this is normally not permissible has always been a significant challenge. It is one thing to use a plasma-arc cutting torch in a steel fabrication shop; it is altogether another matter to do so in a flour mill.
Experience has shown that sparks generated by some hot work processes can fly, roll, bounce, or otherwise travel great distances, such as beyond 15 metres (50 feet). Incidents are known to have occurred where sparks have initiated smouldering fires that have gone unnoticed for many hours before progressing to a full combustion stage.
The newly revised edition of CSA W117.2:19 has updated requirements for fire watch, site preparation, and fire protection. Additional recommendations for fire and explosion prevention precautions are included in an informative annex.
Electrical hazards
A disturbing cluster of preventable electrocution and electrical shock incidents related to arc welding have occurred in Canada in recent years. These incidents can be grouped into two general categories: secondary voltage hazards and stray welding current damage.
The secondary (or output) voltage on many arc welding machines is high enough to electrocute a person when the conditions are unfavorable. Typically, maintenance workers are at the highest risk because of the nature of the welding processes that they use and the challenging work environments that they endure. The four contributing factors in most welder electrocutions are the following:
- When the work environment is hot, humid, damp or high in electrolytes, and the moisture or worker’s perspiration reduces the electrical insulating properties of standard PPE such as leather gloves or work clothes.
- When the worker is in a confined or restricted space or has the possibility of contacting the work (or structure) that is being welded.
- When the welding machine is producing voltage across the terminals at the upper-end of the regulated limits (e.g., 80 V).
- When the worker is using a process such as shielded-metal arc welding (SMAW) — commonly called “stick welding” — where the welding machine voltage is normally “On” and there is a requirement to routinely touch the electrode to change this consumable.
For these circumstances there is an engineering control called a voltage reduction device (VRD) available that can prevent the shock hazard. VRD technology is available on certain models of new arc-welding machines (from all of the major equipment manufacturers) or they can be purchased as an accessory and easily retro-fitted onto legacy machines. Unfortunately, VRD technology is not well-known by end-users and is not yet in wide-spread use. The revised CSA W117.2:19 now specifies the use of VRD technology under the set of circumstances described above.
Stray welding current damage to electrical systems is a fault condition where not only serious property damage can occur, but where the damage to protective electrical wiring (grounding or bonding wires) can be severe. The magnitude of the electrical current used in welding is much higher than standard electrical circuits are designed to carry and this can ultimately lead to the electrocution of other unsuspecting workers, perhaps even days or weeks after the original incident has occurred. The stray welding current fault can occur after a welder makes a very simple and inadvertent error, which to this person is most likely transparent.
The primary purpose of this standard is to improve the health and safety of welders and other personnel using these processes. The goal is to encourage fresh thinking and attitudes, to increase the awareness of the importance of welding safety, and the need to make continual improvements in the welding environment over time. If your organization uses welding and related processes, it is highly recommended that you obtain an updated copy of CSA W117.2:19 to help proactively guide your occupational health and safety policies, internal training, work instructions and contractor oversight.
Jim Galloway is a professor of welding engineering technology at Conestoga College in Cambridge, Ont. Click hereto view his students' videos on stray welding current scenarios. Before joining the faculty at the college, he worked in nuclear power-plant construction, welding research and development and as a technical and manufacturing manager overseeing heavy steel welding and fabrication work. Galloway also volunteers as a technical member on several Canadian Standards Association committees including CSA W117.2 Welding Safety.