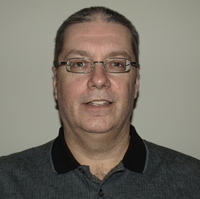

The supervisor/worker relationship, in this author's opinion, is the most important link in the organizational structure to ensure safety is being addressed in the workplace. A weak relationship at this level can make safety issues more difficult to be resolved due to workers having inadequate direction or expectations.
Problems or issues that are not properly addressed can lead to disgruntled employees. This could result in workers initiating work refusals.
Understanding the internal responsibility system (IRS) is one thing, however, applying this system in your day-to-day work activities presents many challenges.
We all know that the IRS is a system, based on values and principles, which enables everyone in an organization to be directly responsible for health and safety, regardless of their position within their company. Simply put, it is the “people” component of your health and safety managed system.
The IRS can be used to assist the supervisor/worker interface when it comes to identifying and resolving safety issues.
The following four step process can be utilized by the supervisor and workers as a method of addressing safety issues (Figure 1 - click on image for larger view):

Step 1 – Prevention
Good line organization interactions are the building blocks for the prevention of accidents. The manager must have safety programs in place to assist the line organization in achieving their safety goals. Authority must be given to supervisors in order for them to exercise their legal and corporate duties. The manager must communicate safety expectations to the supervisor on a regular basis.
The supervisor, in turn, must ensure that the safety expectations are clearly understood by the workers and that achieving them is possible through proper job safety planning. The supervisor can accomplish this by assigning the tasks to competent workers and to advise them when issues arise during work execution.
The workers should be trained in identifying safety issues through the use of hazard awareness techniques such as energy analysis and job safety analysis.
Energy analysis consists of assessing the different energy sources and the inherent hazards associated with each job. Here are some examples:
• electrical energy = electrocution
• mechanical energy = pinch point, crushing
• thermal energy = burns
Job safety analysis consists of breaking the job steps in sequence, identifying the hazards and addressing the hazards with effective controls or barriers. Here are some examples of barriers:
• isolation (lock out/tag out)
• procedures/work instructions
• personal protective equipment
Using these types of techniques will enable the workers to plan safety into each of their jobs by helping them identify and control the hazards associated with the work.
The workers are then able to assess the work on a daily basis and correct any deficiencies that are within their immediate control without the need for supervisory intervention.
Step 2 – Reporting
Reporting must occur when the workers determine that they cannot address the workplace safety issue by themselves. This could include observing contraventions or conflicts in other work groups.
There are legal requirements in Canada to report to the employer or supervisor any contraventions of safety regulations or the existence of any hazard known by the worker.
Many employers also have corporate requirements obligating workers to report any hazards, unsafe activities and unsafe acts to their supervisor.
The reporting of safety issues can be made formally through a written report but could also be done during the job planning process, at tailboard conferences or at group safety meetings.
Step 3 – Problem solving
Once an issue has been reported by the worker to his/her immediate supervisor, there is a need to address and correct the problem collectively.
The following method is one example of a problem solving process (Figure 2 - click on image for larger view):

1. Identify the issue
• Accumulate all of the facts and information related to the issue. Be sure to provide as much detail as possible to clearly reflect the problem.
• Include any actions taken to mitigate the hazards.
• Document the situation in writing for future reference.
2. Determine the causes
• Determine the contributing factors that are creating the issue.
• Perform an analysis of these contributing factors.
• Determine the root causes.
3. Suggest improvements
• Together, the workers with the supervisor develop ideas to improve the situation.
• You may want to get help from your company’s internal resources such as the site H&S advisor, the local JHSC or the corporate safety/wellness group.
• Suggestions must be practical to effectively address the situation.
4. Take action
• Develop a corrective action plan to deal with the issue’s resolution.
• Review all actions required by the line organization and the specific work group to ensure that the work has been properly planned for execution.
• Initiate the corrective action plan.
• Upon completion, perform a corrective action follow-up to determine that the plan was successful in addressing the issue.
Step 4 – Intervention
The last step is really only required if the supervisor and workers are not able to deal with the problem. This is often the case when the issue is caused by factors that are not in the work group’s control such as engineering design issues.
The supervisor will require assistance from his/her line organization in order to resolve the issue. This could include the need for an engineering review, a cost analysis (budgeting) and a formal planning/scheduling process.
There are also other groups that can assist the supervisor and workers in resolving safety issues. They are:
• the company health & safety professional
• the joint health & safety committee
• external safety consultants
• safety associations
Each of these groups can help identify and promote safe work practices as well as determine any legal requirements involved.
Intervention may require your company’s head office or corporate group for longer term, corporate, industry wide and legal issues. The bigger the issue, the more intervention will be required from the line organization.
The need for intervention can really be summed up in the definition of IRS: “Everyone in an organization is directly responsible for health and safety, regardless of their position within their company”.
It is important that the supervisor maintain an effective relationship with his/her workers to help promote the IRS. This will go a long way towards preventing potential problems from becoming bigger ones. It will also help create a working environment that is both respectful and engaging to the employees.
Guy Chenard, CRSP, C.E.T., is a safety professional with Ontario Power Generation.