Some printers produce a large amount of particles, causing respiratory symptoms in workers
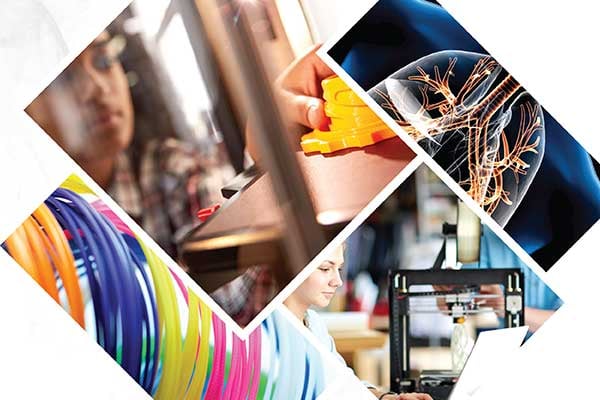
Brent Stephens was teaching a graduate class on the physics and chemistry of indoor air pollution in 2013 when a student mentioned to him that the 3D printers in the shop where he worked were giving off a funny smell. The smell was of burning plastic, the student told his teacher, who decided to investigate and launched a study on the matter.
“A 3D printer takes a piece of plastic filament and forces it through a hot nozzle. It’s definitely emitting gases and that’s probably what you are smelling. But then there’s also probably some particle emission, probably ultra-fine,” says Stephens, associate professor in the department of civil, architectural and environmental engineering at Illinois Institute of Technology in Chicago.
Three-dimensional (3D) printing is the process of making a physical object from a computer-generated image, typically by laying down many thin layers of material (or filaments) in succession. The applications of 3D printing are growing all the time. Objects printed in 3D are already found in many industries, including aerospace, automotive and military. In health care, 3D printing is used to produce medical prostheses as well as orthopedic and dental implants. Besides large commercial 3D printers, smaller desktop versions are becoming more commonplace as well, turning offices into small-scale manufacturing facilities.
But studies have shown that commercially available printers produce large concentrations of ultra-fine emissions, some of them containing hazardous substances. Once inhaled, these particles are deposited in the lungs, where they may cause inflammation, headaches and adverse cardiovascular effects. Taking steps to reduce the indoor air pollution produced by 3D printers and following a health program can help maintain cleaner, healthier air for workers.
A recent study conducted by the Centre for Research Expertise in Occupational Disease (CREOD) in Toronto concluded that regular exposure to 3D printers poses significant adverse respiratory heath effects. For the study, the centre surveyed 46 workers at 17 workplaces to collect data on their occupation and health status, such as symptoms, diagnoses and family history. The study had several main findings.
Working full-time (more than 40 hours a week) with 3D printers is associated with various negative health effects. Among workers who operated 3D printers:
• 57 per cent experienced respiratory symptoms more than once a week in the past year
• 22 per cent had physician-diagnosed asthma
• 20 per cent experienced headaches
• 20 per cent had cracked skin on their hands.
Few workers use personal protective equipment (PPE). Among workers who operated 3D printers:
• 48 per cent used PPE
• 37 per cent used skin protection
• 35 per cent used respirators or masks.
Injuries were also reported. Among workers who used 3D printers, 17 per cent reported injuries, which were most often cuts or scrapes.
The study conducted by Stephens and his research group in 2013 measured particle concentrations and emission rates resulting from standard, commercially available 3D printers inside a typical office. They found printers using acrylonitrile butadiene styrene (ABS) filaments were more dangerous to the health of workers than polylactic acid (PLA) filaments.
“We showed that both types of printers emitted a large number of ultra-fine particles. And also, one type of printer filament (ABS), used in a printer operated at a higher temperature, emitted 10 times as many particles as the other type that we tested,” Stephens says.
In 2016, Stephens and his students tested emissions of particles and gases to determine the quantity and type of volatile organic compounds (VOCs) being emitted. They tested emissions produced by five different types of printers and a wide variety of filaments, testing up to nine filaments in one type of printer alone. That testing led to two important findings.
First, they found that several of the printers using ABS filaments emitted styrene, a VOC that is considered by some regulatory bodies, including the International Agency for Research on Cancer (IARC), as a possible human carcinogen.
“That’s generally known to be not a great thing that you want in indoor environments,” Stephens says. “We searched around in different databases. We found some studies that estimated that high concentrations (of styrene) are likely to have some long-term cancer potency that may be worth looking at.”
Stephens also came across a study that associated very low levels of styrene with a risk of pulmonary infection.
Second, their study showed nylon filaments emitted a compound called capralactum, a water-soluble compound used to produce a type of nylon. The presence of this compound can present a health risk, depending on the printer and filament being used.
Stephens says capralactum is listed by the Office of Environmental Health Hazard Assessment (OEHHA) in Sacramento, Calif., which advises a very low chronic exposure level. Thus, it is a cause for concern that, when his research team operated a printer with nylon filaments in a typical office environment, the capralactum emissions exceeded those levels.
“You can very easily with some of these printers go over that level,” he says.
According to the Centers for Disease Control and Prevention (CDC) in Atlanta, acute exposure to high concentrations of capralactum may be irritating to the eyes and respiratory track and may cause effects on the central nervous system.
Some 3D printers use photopolymers, a polymer that cures, or becomes solid, when exposed to light, typically laser or UV. Many of these photosensitive liquid resins are toxic, says Kerry Stevenson, founder and editor at Winnipeg-based Fabbaloo, a blog devoted to 3D printing. Although some cartridges of photopolymers carry warning labels, most people still do not understand these resins can be toxic.
“You find people merrily using these things. They pull the objects out of the machine and they’re solid. But they’re also wet with liquid material that has not been cleaned off. A lot of printers have an alcohol system to dissolve off this resin, but the substance can be toxic. Some of it is food grade, but a lot of it isn’t,” he says.
As a result, any worker handling these resins should wear gloves, at least, to prevent it from getting on the skin. In some situations, Stevenson advises, it may also be a good precaution to wear a respirator or make sure the workplace is ventilated.
Metal printing, typically done with a very fine metal powder, can also produce a respiratory hazard. The metal is placed flat on a powder-bed, metal 3D printer, and operators use a high-powered laser to melt it. By repeatedly adding layers of powder and melting and fusing them together, operators build up the object.
To produce a finely resolved object, however, the process requires a very fine powder and focused laser. The powder can become airborne and workers then risk inhaling metal particles, which can harm health because many of them are highly toxic, Stevenson says.
Moreover, the metal powder is often explosive. Powdered titanium and powdered aluminum, for example, are common 3D printing powders and are both highly flammable. While there is no danger during printing, which is usually done in a sealed chamber purged of oxygen, the powder must sometimes be handled outside the chamber. Proper procedures for cleaning powder off the finished object and for recovering residual powder must be followed.
VENTILATION AND FILTRATION
Some 3D printer manufacturers have built controls into the equipment designed to limit particle emission. These controls include covers, full enclosures and filtration systems. Some printers are entirely contained within an enclosure equipped with a re-circulating filter. One company says the filtration system attached to its printer enclosure captures 85 per cent of emissions.
Safety managers should always take advantage of these manufacturer-supplied controls, says Neil Johnston, interim president and CEO of the Manitoba Lung Association in Winnipeg. If the printer comes with an enclosure, it should not be modified.
“Printers usually come in a plastic housing with a hatch that you would access. So those should be maintained and kept in good condition. Make sure the seals are still there and don’t bypass any safety guards — like taking the safety guards off any kind of saws. The safety cabinet needs to be kept in place and maintained or enhanced,” he says.
Workplaces should also reduce emissions by good localized ventilation, Johnston adds. A good high efficiency particulate air (HEPA) system with activated carbon or similar type of filter should be placed near the printers. Make sure printers are operated in a well-ventilated room and install direct ventilation to draw emissions away from the printers and out of the room.
Along with using manufacturers’ controls and installing good ventilation, the National Institute for Occupational Safety and Health (NIOSH) in Atlanta recommends these ways to reduce emissions:
• Maintain a distance from the printer to minimize breathing in emitted particles and choose a low-emitting printer and filament when possible.
• Avoid staying in the same room with a printer for long periods of time.
• Turn off the printer if the printer nozzle jams and allow it to ventilate before removing the cover.
• Use engineering measures first, such as manufacturer-supplied equipment and proper ventilation, then use materials with lower emissions.
• Wear protective equipment such as respirators if necessary.
Managers must also provide proper training, Stevenson says. Workers should be aware of the respiratory hazards created by 3D printers and know how to avoid them.
AIR MONITORING
According to industry recommendations, workplaces using 3D printers should have an air monitoring system to identify the types of emissions the printers are producing and what health risks the emissions may pose to workers.
While the air around 3D printers should be monitored for emissions, the cost may be too high for most companies, Stephens says. An employer who needs “speciated VOC” data, that is, data that identifies the specific VOCs in a sample, would probably have to pay about $400 per sample for an analysis. The instruments that measure the ultrafine particles (UFPs) generally cost at least $6,000 to $7,000. The cost is high because of the small size of the particles, he says. They cannot be measured with the cheaper devices that measure larger particles.
A cheaper option is to do real-time VOC measurement using an instrument such as a photo-ionization detector (PID). The device, which costs about $1,000, is commonly used by occupational health and hygiene managers, Stephens says. While the device will not identify the specific VOCs present in emissions, it will provide the user with a number indicating the total VOCs (TVOC). In their research, Stephens and his team used a PID to measure emissions produced by a printer already tested and identified as containing styrene.
“If you know what your printer is emitting, you could technically use a cheaper instrument like that and get some idea of the VOC concentration. The instrument won’t tell you what the VOC is, and so without knowing what the VOC is, it doesn’t really help you because it might be something harmless,” he says.
RESPIRATORY PROTECTION
If workers are accessing the printer cabinet regularly, Johnston says, they should wear respiratory protection.
“And if the local ventilation is inadequate, they need to have a particulate respirator. That’s the last step after having engineering controls,” he adds.
Whether workers need to wear respiratory protection depends on the type of filament being used in the printing process, Stephens says. Current research shows that ABS and nylon filaments have high emissions of gases or particles, while PLA (polylacticacid) filaments generally do not.
While companies are advised to operate 3D printers in a well-ventilated space, they should be aware that workers situated near the printer for a long time still need to wear some PPE. The main thing here is to make sure the PPE contains a good, combined particle and gas filter, Stephens says, adding 3D printers should be thought of as another shop tool.
“There are a lot of shop tools that, when they’re being used, we generally recommend some kind of protection, whether it’s respiratory masks for sawing or cutting wood or doing laser cutting. I think 3D printing should be lumped into one of those categories — even though it feels a little like a laser printer — particularly if a worker is susceptible (to respiratory health problems),” he says.
INTRODUCE A HEALTH PROGRAM
The employer or safety manager at a workplace using 3D printers should put in place and maintain a health program to ensure emissions are not harming workers, Johnston says. As with any dust and particulates exposure program, it is good to start with a health questionnaire to determine workers’ respiratory health. If any employee has problems, that person might have to go for spirometry (lung-functioning testing) or a chest X-ray. Then, following a good particulate and dusty environment protocol, the manager should check from time to time to see whether there are any changes in the worker’s respiratory health.
Any workers who have allergies, asthma or other chronic lung conditions will be at risk, and added measures may need to be taken.
“People may already have lung problems; those will be exacerbated and those need to be managed. But there are also people who, on exposure to this, may develop lung problems. So there should be some kind of monitoring program as well,” Johnston says.
Today, 3D printing is still fairly new and manufacturers have not paid adequate attention to safety hazards, Stevenson says.
“It’s a very competitive space. Right now, there are a billion companies, and we don’t know which will survive and become the Fords and GMs of the future. They are typically chasing the most prominent aspects in the minds of the customers, which are cost and speed and types of material that are available. Safety is almost never mentioned as an issue,” he says.
Stephens agrees most manufacturers are not focused on developing technologies to reduce emissions. While there are currently many groups conducting environmental and health studies on 3D printers, he says, it would be better if manufacturers focused more on coming up with ways to protect workers’ health.
“I’d rather us not spend resources on measuring emissions,” he says. “I’d rather see this pretty clever group of people — who figured out how to print things — to just say this is probably a problem. Let’s handle it.”
Linda Johnson is a freelance journalist based in Toronto.
This article originally appeared in the February/March 2018 issue of COS.